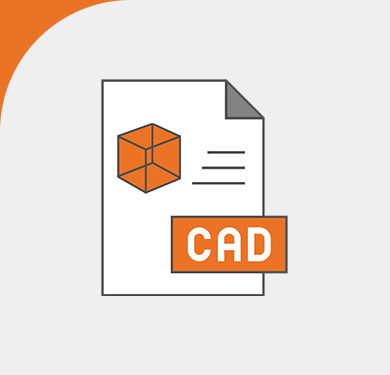
カスタマイズされたプラスチック射出成形図面は、顧客の特定の要件と製品設計に基づいて作成された特殊な設計図です。これらの図面には通常、プラスチック射出成形プロセスに必要な金型設計と製造のガイドとして使用される 2D および 3D CAD モデルが含まれます。
カスタマイズされた図面は、製品の寸法、形状、構造、その他の技術的詳細を正確に描写し、プラスチック部品またはコンポーネントの最終生産が顧客の要件を完全に満たすことを保証します。
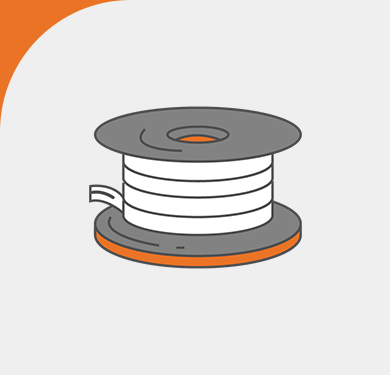
射出成形では、プラスチック金型の設計と選択、およびプラスチック材料の選択が非常に重要です。これらの要素は、品質、コスト、生産効率に直接影響します。
まず、金型設計により、欠陥を最小限に抑えながら製品の精度と一貫性が確保されます。適切に設計された金型は、生産効率を最適化し、コストを削減します。
第二に、適切なプラスチック材料を選択することは、製品の性能、外観、コストにとって重要です。材料によって強度や特性が異なり、技術要件や製造コストに影響します。適切な材料を選択すると、製品の重量も軽減されます。
製造プロセスは、ラピッドプロトタイピングのための 3D プリントから始まり、その後に射出成形金型の製造が続きます。3D プリントにより、製品設計を迅速に評価できます。射出成形金型 (通常は金属製) は、大規模生産に使用されます。このプロセスでは、ラピッドプロトタイピングの利点と従来の射出成形を組み合わせて、効率的な製品開発を実現します。
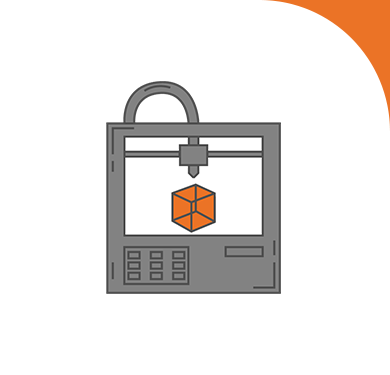
初回品検査とテストは、射出成形プロセスにおける重要なステップです。通常、製造の初期段階で実施されるこの検査により、製品が設計要件と品質基準を満たしているかどうかが検証されます。最初に、サンプル セットが製造ラインから抽出され、外観と寸法を確認するための目視検査と寸法テストが行われます。次に、製品が正しく動作し、期待される機能を満たしているかどうかを確認するための機能テストが行われます。これには、圧力テストや耐久性テストが含まれる場合があります。最後に、結果を定義済みの基準と比較し、製品の品質を確認します。不合格の場合は、プロセスの安定性と製品の一貫性を確保するために、さらに調査と是正措置が講じられます。
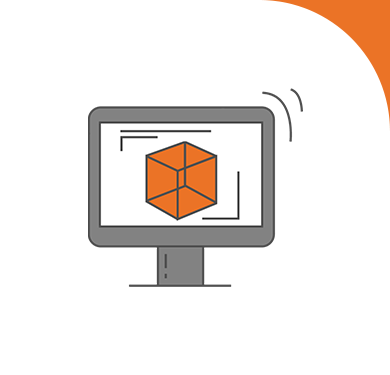

射出成形金型の表面処理とフラッシュは、射出成形製品の外観と表面品質を向上させることを目的としたプロセスです。表面処理には、研磨、メッキ、窒化などのさまざまな技術が含まれており、金型表面の光沢、滑らかさ、耐久性が向上し、射出成形製品の表面がより滑らかで均一になり、見た目も美しくなります。一方、フラッシュは、金型表面に形成される欠陥を指し、多くの場合、不適切な表面処理または操作が原因です。製品の外観と品質に影響を与える可能性があり、最終的な射出成形製品の品質を確保するために、タイムリーな修理と処理が必要になります。
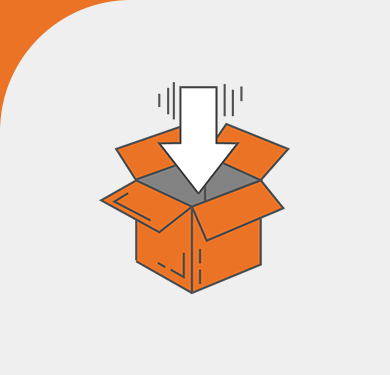
最終製品の梱包確認は、製造後の重要なステップです。製造業者は、梱包が規定の基準と要件を満たしているかどうか検査します。これには、外観に損傷がないか、ラベルが正しいか、必要な書類と付属品がすべて揃っているかの確認が含まれます。目的は、輸送中および保管中に製品が安全に損傷なく顧客に届くようにし、損傷を防ぎ、顧客満足を確保することです。