
Customized plastic injection drawings are specialized blueprints created based on the specific requirements and product designs of the customer. These drawings typically include 2D and 3D CAD models, which are used to guide the mold design and manufacturing required for the plastic injection process.
Customized drawings accurately depict the dimensions, shapes, structures, and other technical details of the product, ensuring that the final production of plastic parts or components fully meets the customer's requirements.

The design and selection of plastic molds, along with the choice of plastic materials, are critical in injection molding. These factors directly impact the quality, cost, and production efficiency.
Firstly, mold design ensures product accuracy and consistency while minimizing defects. Well-designed molds optimize production efficiency and reduce costs.
Secondly, selecting the right plastic material is vital for product performance, appearance, and cost. Different materials offer varying strengths and properties, influencing technical requirements and production costs. Proper material selection can also reduce product weight.
The manufacturing process starts with 3D printing for rapid prototyping, followed by injection mold production. 3D printing allows quick evaluation of product design. Injection molds, typically metal, are used for large-scale production. This process combines rapid prototyping advantages with traditional injection molding for efficient product development.

First-article inspection and testing are crucial steps in the injection molding process. Typically conducted early in production, this inspection ensures products meet design requirements and quality standards. Initially, a sample set is extracted from the production line for visual inspection and dimensional testing to verify appearance and dimensions. Functional testing follows to ensure products operate correctly and meet expected functionality, which may include pressure and durability tests. Finally, results are compared to predefined standards to confirm product quality. If failed, further investigation and corrective actions are taken to ensure process stability and product consistency.


Injection mold surface treatment and flash are processes aimed at improving the appearance and surface quality of injection molded products. Surface treatment involves various techniques such as polishing, plating, and nitriding to enhance glossiness, smoothness, and durability of the mold surface, resulting in smoother, more uniform, and aesthetically pleasing surfaces of injection molded products. Flash, on the other hand, refers to defects formed on the mold surface, often due to improper surface treatment or operation. It may affect the appearance and quality of products, necessitating timely repair and treatment to ensure the quality of the final injection molded products.
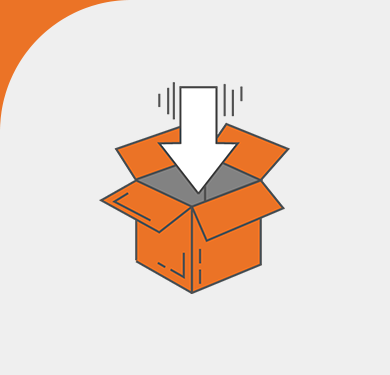
Final product packaging confirmation is a crucial step after production. Manufacturers inspect to ensure packaging meets set standards and requirements. This includes checking for intact appearance, correct labeling, and inclusion of all necessary documents and accessories. The aim is to ensure products arrive safely and intact to customers during transportation and storage, safeguarding against damage and ensuring customer satisfaction.